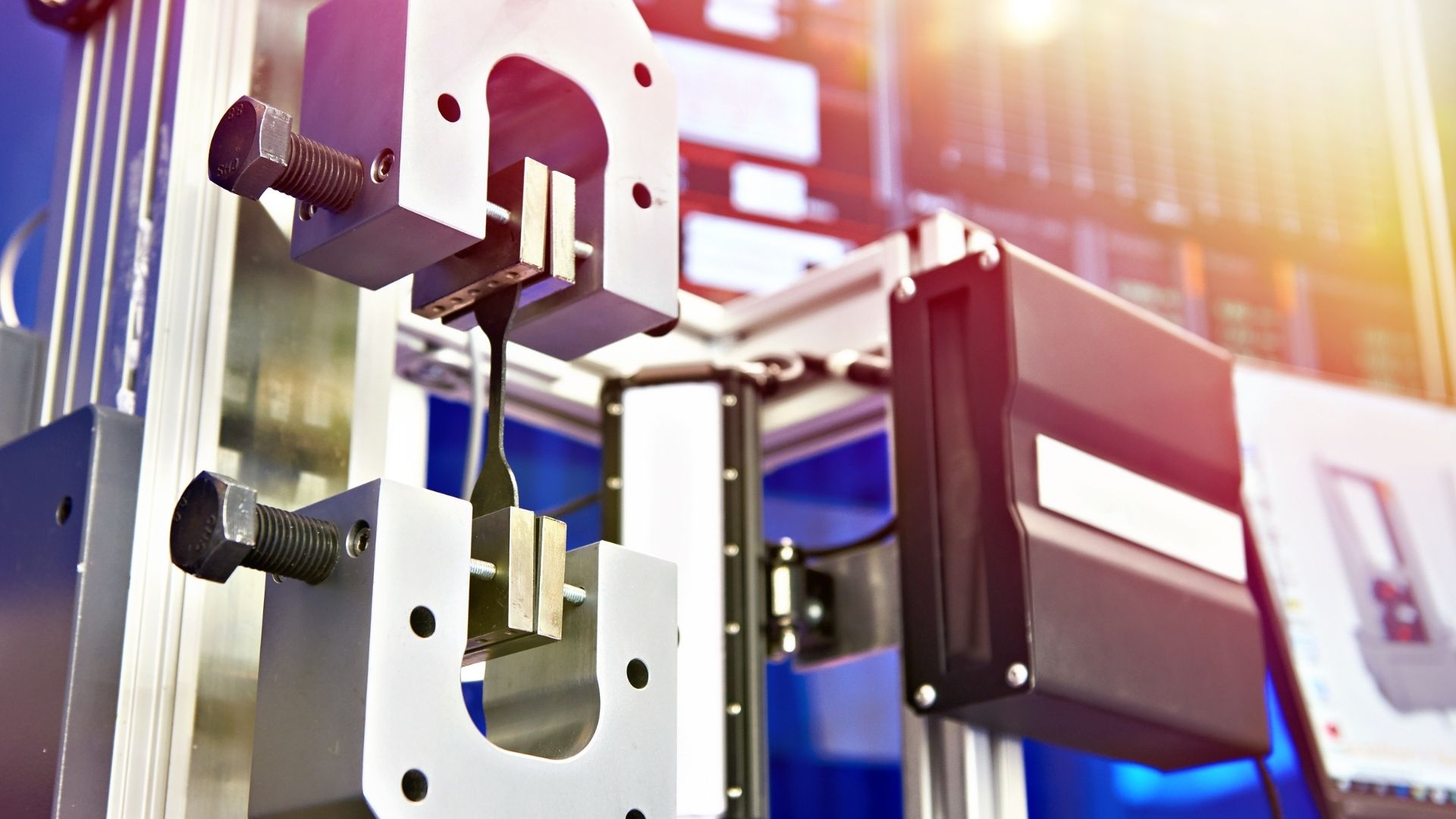
At All Metals Fabricating, we understand that efficient manufacturing is critical to meeting deadlines and controlling costs. We’re committed to efficiency at every stage of production. Today, we’re focusing on one of the most important yet often overlooked phases: assembly.
The assembly phase can significantly reduce your timeline with only a few strategic adjustments to your project. Our expert assemblers are ready to guide your parts through this phase swiftly with an optimized design and proper guidance.
Utilize these 7 tips to streamline your assembly process and unlock substantial time savings.
Many projects assign separate part numbers to every component, including hardware. For instance, a bracket may be A1, and its PEM fastener is A2. This common practice requires multiple travelers to move through our shop, and every new traveler increases costs and slows down a project.
Instead, we recommend including your hardware on the part level, reducing the number of travelers required. This will not only decrease the price of your assembly but will also enable faster production times.
Whenever feasible, we recommend customers select imperial hardware sizes. These are more readily available in the United States, which helps prevent project delays as we wait for less common hardware. If your project requires metric hardware, we advise using metric sizes exclusively within a single assembly.
For maximum efficiency, we recommend using ¼”-20 throughout your projects. This hardware offers two key advantages:
By using a consistent hardware size throughout your project, assemblers will not need to search for a variety of corresponding screws, washers, or bolts, enhancing their overall productivity and allowing your project to be delivered more quickly.
Clear, detailed assembly instructions can greatly improve production speed and prevent potential issues. We encourage you to “think like an assembler” during the design phase. Providing blueprints with step-by-step guidance allows our team to identify any potential challenges before they arise, ensuring a smoother assembly process.
A seemingly minor detail, like a hard-to-reach screw hole, can become a significant bottleneck. By offering clear instructions, you’ll eliminate surprises and speed up assembly.
Assembly is not the end of your product’s journey – it still must be shipped safely to its destination. We encourage customers to incorporate shipping plans into a product to prevent any risk of damage, including considerations such as:
When considering finishing requirements, think about the visibility and function of each part in the final product. Interior parts that aren’t visible may not need high-quality finishes, allowing you to save on costs. For example, some customers use galvanized or unfinished aluminum or stainless steel on internal parts.
By assigning finishes based on the function of each component, you can reduce expenses without sacrificing quality.
The strategic placement of hardware is essential to structural integrity and smooth assembly in metal fabrication projects. Improper positioning, particularly near bend lines or edges, can potentially lead to manufacturing challenges and compromise the quality of your final product.
We recommend customers refer to hardware manufacturer specifications for proper placement of holes. This will lead to efficient assembly and a structurally sound final product.
Involving us early in your project can lead to more successful outcomes. A quick consultation with our team can help you optimize your design for cost-efficiency and a smoother assembly. Our years of industry experience allow us to provide valuable guidance that keeps your project on track.
At All Metals Fabricating, our collaborative approach to every phase of manufacturing enables more successful projects. Whether you need sheet metal fabrication, CNC machining, finishing, or any of our broad capabilities, we leverage our expertise to help you minimize project costs, accelerate timelines, and achieve high-quality results.
From optimizing part designs to providing insights on hardware selection and assembly techniques, we are committed to equipping you with the knowledge and tools you need to succeed. Whether you have specific questions or need guidance on best practices, we’re here to help you navigate the complexities of your assembly and ensure that your project moves swiftly through the production stages.
Request a quote today.