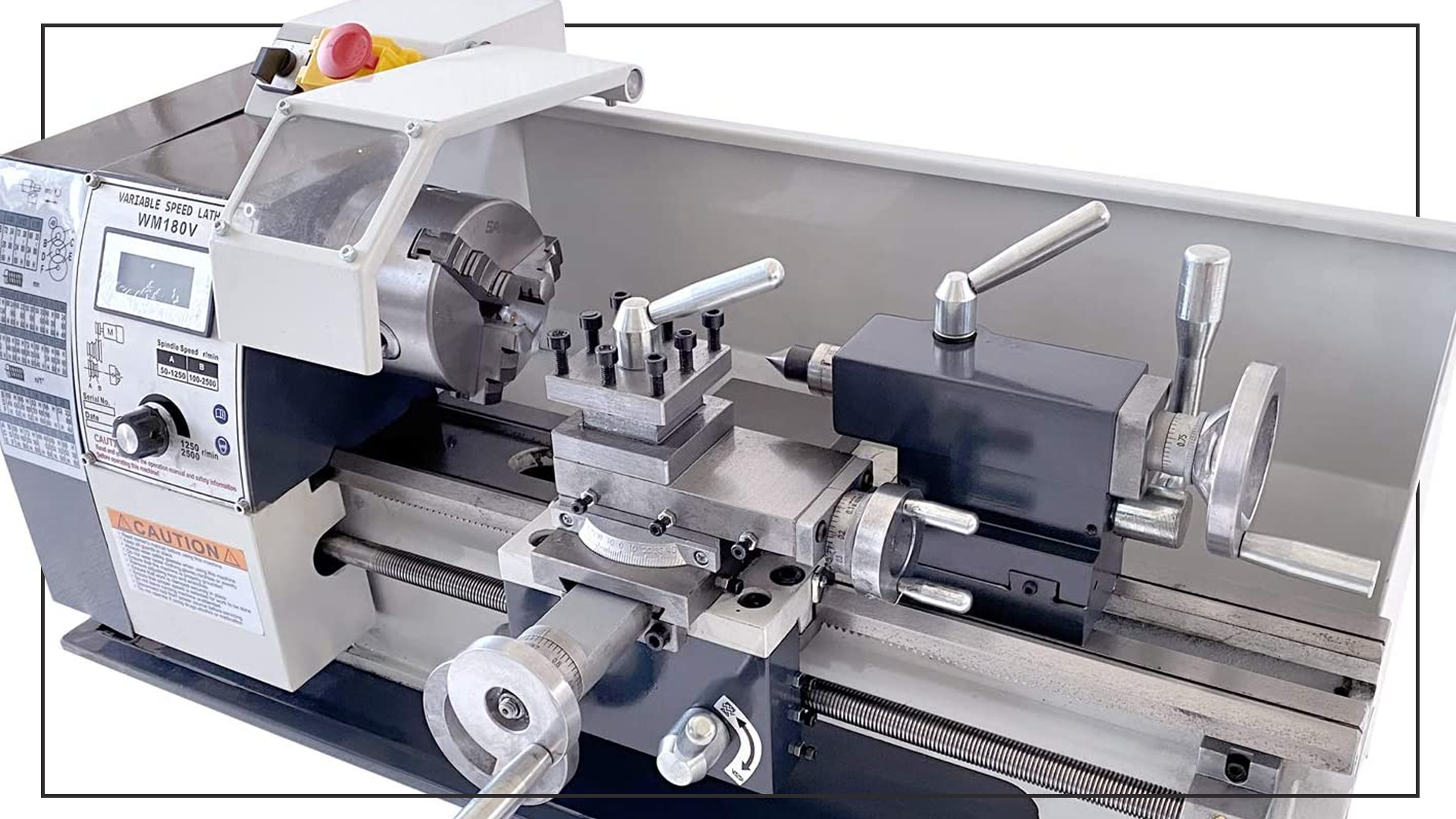
Lathes are essential tools in modern metal fabrication, with a history dating back to ancient times. The Egyptians first developed a rudimentary lathe around 1300 BCE, and by 1569, the French had refined its design into a more modern form.
Today, CNC lathes are capable of producing precise and intricate components for demanding industries such as aerospace, oil and gas, and medical. At All Metals Fabricating, we leverage advanced CNC lathe technology to ensure that our customers receive the highest quality parts with superior precision, versatility, and efficiency.
We proudly use top-of-the-line CNC lathes in our Texas manufacturing facility, enabling us to offer faster turnaround times and tighter tolerances. Whether you need shafts, connectors, housings, or custom components, our state-of-the-art equipment allows us to meet your exact specifications, every time.
At All Metals Fabricating, we operate three advanced CNC lathes:
Our lathes come equipped with advanced features like dual spindles and live tooling. These innovations allow us to offer:
At All Metals Fabricating, our investment in advanced CNC lathe technology enables us to tackle complex, high-precision machining projects across a wide range of industries. Our skilled team combines decades of experience with cutting-edge capabilities to deliver solutions that meet your exact requirements. From prototype work to large-scale production, we provide manufacturing solutions optimized for efficiency and quality.
We’re proud to be a leader in both sheet metal fabrication and CNC machining, with an unwavering commitment to integrity and customer satisfaction.
Request a quote today to see how our CNC lathe services can bring precision and excellence to your next project.
A lathe is a machine tool that rotates a workpiece while a stationary cutting tool shapes it. Primarily used in metalworking, it removes material to create features like threads, holes, faces, and custom designs. Its versatility in shaping parts has earned it the nickname "Mother of All Machine Tools."
How Does a Lathe Work?
A lathe operates on a simple principle, but it has many complex moving parts. Most lathes contain a headstock, tailstock, spindle, motor, chuck, and an assortment of cutting tools. First, the workpiece is fastened to the chuck. This is the part of the machine that holds the piece in place. The chuck usually grips the outside of the workpiece. The spindle, which is attached to the chuck, is connected to the engine that rotates the workpiece. This is the part that allows the workpiece to rotate.
Once the piece is spinning, it's ready for cutting. Then, the machinist attaches a cutting tool to the tool holder. The tool holder keeps the cutting tool firmly in place and allows the tool to travel the length of the piece as it spins. Cutting tools come in a wide variety of sizes, each with its own purpose. Turning tools can cut material off of the workpiece. These flat blades are the most common kind of cutting tool used in lathe work. Other cutting tools include boring bars to make holes larger, chamfering tools to create bevels, and parting tools to cut the workpiece in half.
What are the different types of lathes?
Lathes are an integral part of the manufacturing process and can create a wide range of products. Because of this, some lathes have specialized functions.
These lathes take their name from steam engines that used to power them during the Industrial Revolution. Machinists use engine lathes in metalworking to perform tasks like drilling and boring. These are the most common kinds of lathes used for industrial applications.
Speed lathes are small lathes used in woodworking. These are among the simplest lathes when it comes to their design, as they possess only a headstock, tailstock, and tool turret. They get their name because of their spindle, which is capable of revolving at a high velocity.
Turret lathes have a turret instead of a tailstock. The turret is capable of holding a number of cutting tools, all of which can be used in succession. This allows the operator to produce identical workpieces on the same machine, saving them time and ensuring that each piece is identical.
These lathes are similar in function to the engine lathe but offer a greater amount of control. Tool room lathes are used when the accuracy of cuts is of the utmost importance. They have variable speed control and can spin quickly or very slowly, depending on the operator's needs.
What are the 7 main operations of a lathe?
A lathe is a versatile machine that performs a variety of operations. Some of the most common include turning, facing, boring, threading, knurling, drilling, and parting.
What are the main types of CNC lathes?
CNC lathes are commonly categorized by axis configurations or design types. 2-axis lathes are the most basic configuration, with movement along the X and Z axis, but lathe options include 3, 4 or 5+ axes.
Design types include horizontal lathes, vertical lathes, Swiss-type lathes, and twin-spindle lathes. Each type has specific advantages depending on the workpiece size, material, complexity, and production requirements.
What are the main differences between CNC lathes and CNC turning centers?
CNC turning centers are generally more sophisticated than CNC lathes. Turning centers typically have rotating tools, sub-spindles, larger tool magazines with automatic tool changing, and more than 2 axes.
What is the difference between a lathe and a mill?
In a traditional lathe, the workpiece rotates while the tool remains relatively stationary, producing a cylindrical or round part. In a traditional mill, the tool rotates while the workpiece remains stationary, allowing the creation of a variety of different features.
In modern CNC technology, the line between the two machines can be somewhat blurred, as mill-turn centers combine the two capabilities, and 5-axis machines can perform complex operations.
What materials can be machined on a CNC lathe?
CNC lathes can machine a variety of materials, although each material requires appropriate cutting tools, speeds, and machining parameters. The most commonly machined materials include metals (for instance: steel, aluminum, brass, titanium), plastics (Delrin, Nylon, PEEK, and more), and wood (hardwoods, softwoods, composites).
What type of tooling is used in CNC lathes?
CNC lathes use a wide array of tooling that varies by category, material, and holding system. Common tools include turning tools, boring bars, threading tools, grooving tools, and drill bits, with many other specialized options available for specific operations.
What are common parts manufactured using CNC turning?
CNC turning can produce a wide range of parts. Common examples include shafts, pins, fasteners, bushings, and valve stems, with applications across industries from automotive to aerospace and beyond.