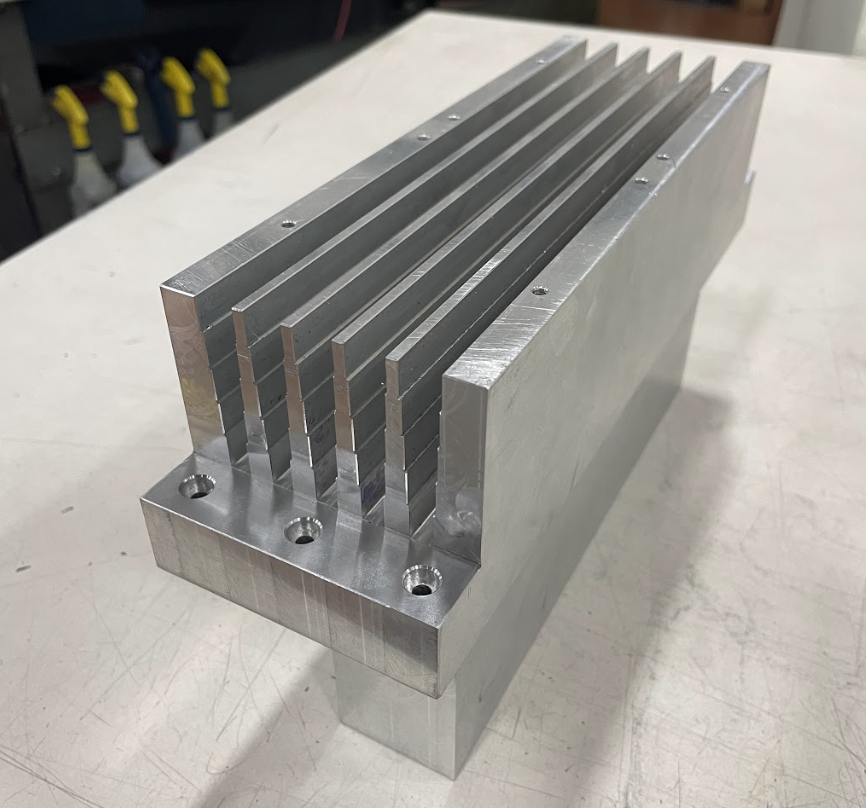
At All Metals Fabricating (AMF), precision and efficiency are at the heart of our manufacturing processes. Tolerances—the permissible limits of variation in a physical dimension—play an important role in ensuring the fit, function, and quality of the final product. Drawing on decades of experience, we regularly engage with our customers to optimize design specifications, reduce production costs, and enhance the performance of their parts by addressing tolerancing issues.
We frequently encounter tolerances that either require adjustment for manufacturability or could be modified to reduce costs and lead times. By understanding the key differences between machining, sheet metal, and welding tolerances, customers can make informed decisions that improve their projects' outcomes.
At All Metals, we specialize in both sheet metal fabrication and CNC machining, which are two distinct processes with different standards in tolerancing. CNC machining tolerances can be much more precise due to the nature of the equipment and processes.
But we occasionally receive sheet metal designs that specify machining tolerances, which is problematic. Unrealistic tolerances require us to go back to customers to discuss changes. That’s time lost for everyone involved. Some shops will simply no-quote a project with impractical tolerances without explaining why. Our team will tell customers why we cannot quote a project so they can make adjustments, if possible.
We can achieve tight tolerances in both sheet metal and machining, but customers should understand that tight tolerances affects cost, because it takes more time to be machined and inspected.
In sheet metal, there are some typical defaults – with a few underlying assumptions – that we printed in the table above. In many cases it’s possible to achieve tighter tolerances, but it’s often dependent on other factors like part geometry. If you’re looking for tighter tolerances in sheet metal fabrication, it’s best to contact us to discuss. When we know the important factors involved in your manufacturing project, we can help you make the best choices possible.
In machining, it’s difficult to give a blanket recommendation for tolerancing. It’s a bit of a sliding scale, heavily dependent on the specific equipment a shop has to both machine and inspect the part. At All Metals, we take pride in the state-of-the-art equipment in our precision machine shop, enabling us to achieve exceptionally tight tolerances. We can even get to the level of microns in certain instances. If your part requires very precise tolerances, we encourage you to reach out to discuss your specifications with us.
In welding, a common tolerance for general fabrication is 1/16”, but there are a range of possible tolerances depending on a variety of factors. At All Metals, we specialize in precision welding services and can often achieve much tighter tolerances by using fixtures. But in welding especially, it’s helpful to avoid making tolerances tighter than they need to be, because tight welding tolerances can drive up costs substantially.
The major recommendation we make is that a part’s form, fit and function should always be considered in assigning tolerances. We recognize that very tight tolerances are sometimes necessary, especially in industries such as aerospace, medical and energy. Some other major factors to consider are:
With sufficient information, we can help a customer determine if a tolerance could be relaxed without compromising functionality. For instance, when we’re manufacturing a component that is part of a larger assembly, it’s helpful for us to have visibility into all of the relevant parts, even if we’re only manufacturing one piece.
At All Metals, we excel at achieving tight tolerances across our wide range of capabilities. Our experienced press brake operators, skilled welders, and cutting-edge equipment enable us to meet precise specifications, surpassing the standards of other sheet metal shops.
However, just because a tolerance is achievable doesn't make it necessary in every instance. It's important to recognize that tight tolerances can significantly impact pricing and may not always be essential for your specific part. At All Metals, we bring extensive experience to the table, particularly in collaborating with customers during the design and engineering phase. This allows us to assist in identifying areas where tolerances can be adjusted without compromising performance or quality. Our goal is to ensure that your project achieves the optimal balance between precision, functionality, and cost-effectiveness.
Partner with AMF to optimize your design and achieve exceptional results for your next project. Request a quote from our team and discover how we can help you achieve more with your next project.