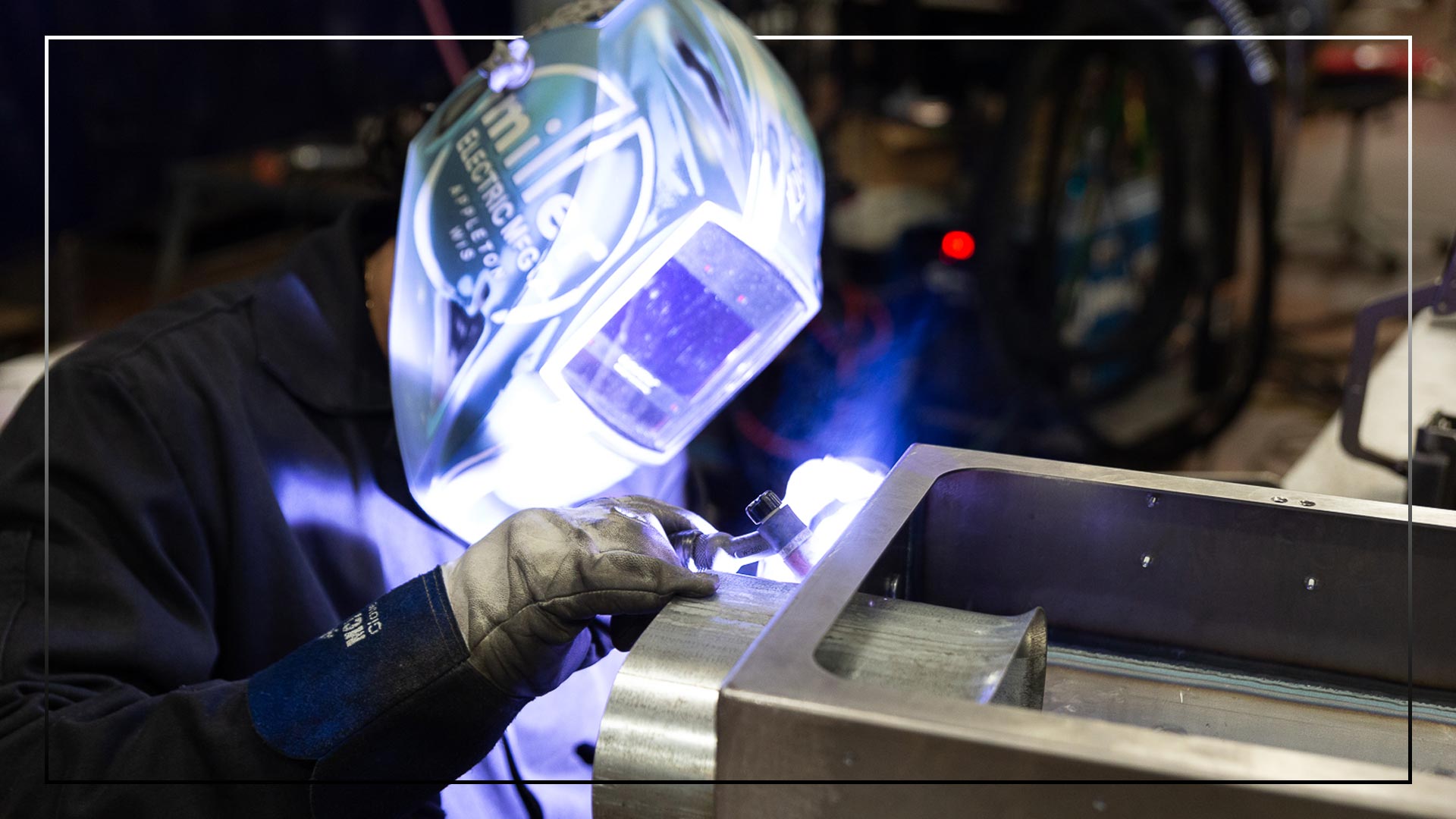
Are you planning a project that involves joining pieces of metal together? Maybe you're wondering what the differences are between soldering vs. welding metal together?
These terms are often used interchangeably in metal fabrication. This can be confusing as each technique is different and has a distinct application.
Deciding which technique is best for your project depends on what you are joining, and how strong you need the join to be. Although both techniques can join metal, it's important to use the right technique for your project.
If you're interested in learning more about the differences between soldering and welding, you're at the right place. This article will explain the benefits of both techniques and their applications.
Soldering is the process of joining two metal components together by melting solder. This soft metal alloy is generally made from a mixture of tin and copper. Depending on the type of solder it has a melting point of between 190 to 840 °F.
This melting point is much lower than the base metal components. During the soldering process, you melt the solder but not the two pieces of metal that you are joining together.
The first step is to clean and position the two pieces of metal you plan on soldering together. You then apply heat with a soldering iron or a gas torch. This melts the solder and connects the two pieces of metal together.
There are many different types of welding but they all involve the same basic principle. If you apply enough heat to the base metal components they will melt and fuse together. The temperature required to melt metal is around 6,500 °F.
A filler material is often used to add some extra metal to the join. These welding rods help to ensure that there is enough molten metal to create a strong connection.
Welding rods contain a non-metallic material called flux. This helps to prevent the molten metal from oxidizing, which weakens the connection. Once a welded connection has cooled it is stronger than the two pieces of base metal.
Depending on the type of welding there are a few different ways of producing the required heat. Electrical welding machines use a high-current arc to melt the metal. Oxyacetylene gas torches use an intense flame to heat up and melt the metal.
Soldering allows you to join a range of different metals together. These include copper, brass, iron, silver, and gold. It is mostly used to make electrical connections and for non-structural metal connections.
Soldering is commonly used to join together the electrical components on circuit boards. Using solder makes it possible to connect these tiny components without using electrical wire.
Another common application of soldering is in plumbing. Copper pipes are joined together with a leak-proof connection by heating them and using solder to seal the join.
Soldering is also used to make jewelry and musical instruments like trumpets.
A wide range of industries uses welding to make high-strength structural metal connections. Making these structural welds requires a lot of equipment, experience, and skill.
Depending on the type of metals you want to weld together you should use MIG or TIG welding. All welding machines create a bond strong enough to withstand extreme stress.
Some common applications of welding are sheet metal fabrication plants, construction, shipbuilding, and heavy machinery repairs. Production welding supports manufacturing and metal fabrication and is essential for creating every day items.
Welding is used extensively on automobile and aircraft assembly lines. It is also used to connect industrial pipes.
Brazing uses the same technique to join metal together as soldering. The main difference between the two is the temperature required to melt the solder.
For a soldering connection, the temperature must be below 840°F. If the temperature is above that, then it is brazing.
Soldering does not require much experience or equipment to get started. The temperatures required to melt the solder are also fairly low, making it safer for DIY hobbyists.
Another benefit of soldering is that once you have made the joint you can easily melt the solder and separate the connection. This makes it easy to re-do mistakes until you get them right.
The biggest advantage of solder is that it is simple to join different types of metal together. It is also possible to easily join components that have different thicknesses.
If you have any kind of metal fabrication application, then welding is far superior to soldering. By fusing the two metals together you can create a permanent and strong connection.
There are at least seven different types of welding. These specialist welding techniques mean that it's possible to perform high-quality welds in a huge range of applications. This makes welding far more versatile than soldering.
With advances in technology, it is even possible to use robotic welding to ensure that all your welds are perfect.
Soldering and welding both have distinct advantages and disadvantages depending on the application.
Welding produces a much stronger joint than soldering. This makes it suitable for load-bearing and structural metal connections. Soldering only makes a connection as strong as the solder you use.
Welding two different metals together is generally not possible without specialist equipment and techniques. In comparison, soldering with certain types of solder allows you to join any two metals together.
Does your business require metal fabrication and welding? We trust this article has helped you to decide on soldering vs. welding. Joining metal together is something that is best left to professionals.
At All Metals Fabricating, we have an extensive range of welding equipment and services. Our professional welders have an average of 20 years of experience.
We have the expertise to advise you on the best way to fabricate whatever metal requirements you have for your business or home project.
Contact us to request a quote today.