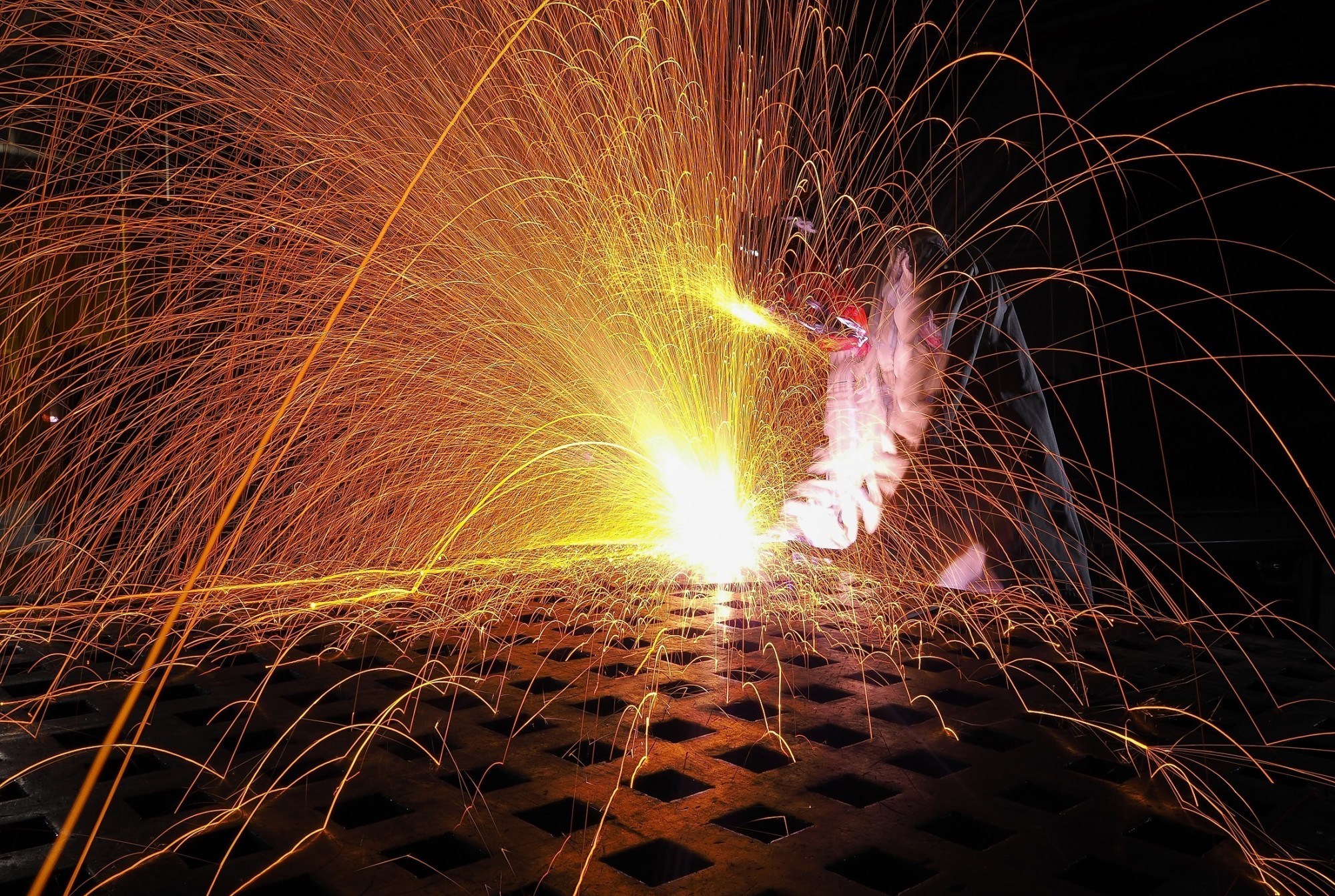
Looking for a high-quality weld? You’ve come to the right place.
At All Metals Fabricating, we pride ourselves on our expert welding team and robust technology. Our shop offers MIG and TIG welding services, laser welding services, and robotic welding services.
A critical element of any welding job is the designing and planning phase, where strategic choices can improve efficiency, cost savings, and component durability. Here are key Design for Manufacturing (DFM) tips to keep in mind when designing parts for a welding project.
Tabs and slots reduce the need for complicated fixtures by interlocking metal parts with tabs on one piece of metal and slots, or holes, on the other. Designing your parts with tabs and slots enables welders to assemble your parts faster and more efficiently. You can also use tab and slot to ensure that parts are orientated correctly prior to being welded together. Essentially these can serve as error proofing the process, while also greatly improving the efficiency of welding them together. Similarly, cleco holes also help the welders locate the exact location to weld parts together, and these holes can be filled in if needed.
When designing an assembly that will require welding, try to keep the sides the same material thickness to avoid heat inconsistencies. For example, if one side is thick and the other is thin, the thinner piece could melt in the time it takes for the welder to heat the thicker piece.
We have deep experience working with different materials and know what it takes to achieve optimal results.
We encourage you to choose your project’s material wisely. For instance, choosing thinner gauge material can pose challenges with preventing warpage due to heat dissipation from the weld. Especially on aluminum, you do not want the material to be too thin and give the welders an issue with warpage.
No matter what material you choose, rest assured that we can handle it!.
While there are techniques we can use to fill gaps, it’s best to start with the smallest gaps possible to enable faster welding.
Not all seams require a complete weld. If you don’t need your seam fully welded, opt for an alternative like skip welding to save time and protect your part from warpage.
We can absolutely grind down welds to create a smooth finish. Just know that this process adds to a project’s cost and lead time and can ultimately weaken the weld. We always recommend opting for strength and durability over an aesthetically perfect finish when possible.
While we are able to hold tight tolerances across welds through the use of robust custom fixtures, that adds time and additional cost to your parts. General tolerancing across welded parts is generally .125”, but we are able to hold as close as .010”-.020” through the use of fixtures. Bottom line is do not have the tolerance any tighter than you need it to be.
Incorporating DFM best practices is one part of the equation. But it’s equally important to work with a shop that offers the right welding technology for the job.
AMF’s welders regularly use six welding techniques: MIG welding, TIG welding, fuse welding, spot welding, laser welding, and robotic welding.
Metal inert gas (MIG) welding is highly efficient but produces a less polished final appearance than other welding techniques. MIG welding is also hard to control, so we don’t recommend it for materials vulnerable to heat distortion, like thin-gauge metals.
TIG welding is slower than MIG welding but creates a stronger weld with greater penetration resulting in a more polished appearance. There is also more control over the welding area than with MIG welding.
Robotic welding is a highly efficient method of automated MIG welding. Robotic welding services are approximately 8-10x faster than manual welding and are ideal for high-volume MIG work requiring long welds.
Laser welding services have only been around for a few years and are a highly efficient alternative to traditional TIG or MIG welding. Essentially this new technology allows you to provide tig weld quality beads at the speed of mig welding!
AMF recently welcomed a new laser robot welder into our sheet metal shop. A major advantage of this machine is that it transfers minimal heat, which proved valuable for a recent project.
This project required us to weld batteries together in a chain to make a larger battery for a small cell site connected to solar panels and a wind turbine. Since the heat transferred with traditional welding methods would have caused the batteries to overheat and damage the battery, we had the opportunity to explore and ultimately purchase a newer and better technology.
With our laser robot welder, we were able to produce a consistent and strong weld without transferring too much heat to the battery. Truthfully, we could never have achieved such a high level of accuracy or consistency with manual welding methods. We can’t wait to put this automated manufacturing solution to work on future projects!
At AMF, our customers’ needs regularly drive our business decisions. We’re always excited about the chance to expand our capabilities.
AMF is confident our sheet metal shop has the best welders in Texas.
Whether we’re offering DFM guidance or investing in advanced technology, we’re committed to doing what it takes to make your welding projects successful.
Request a quote for our precision welding services today.