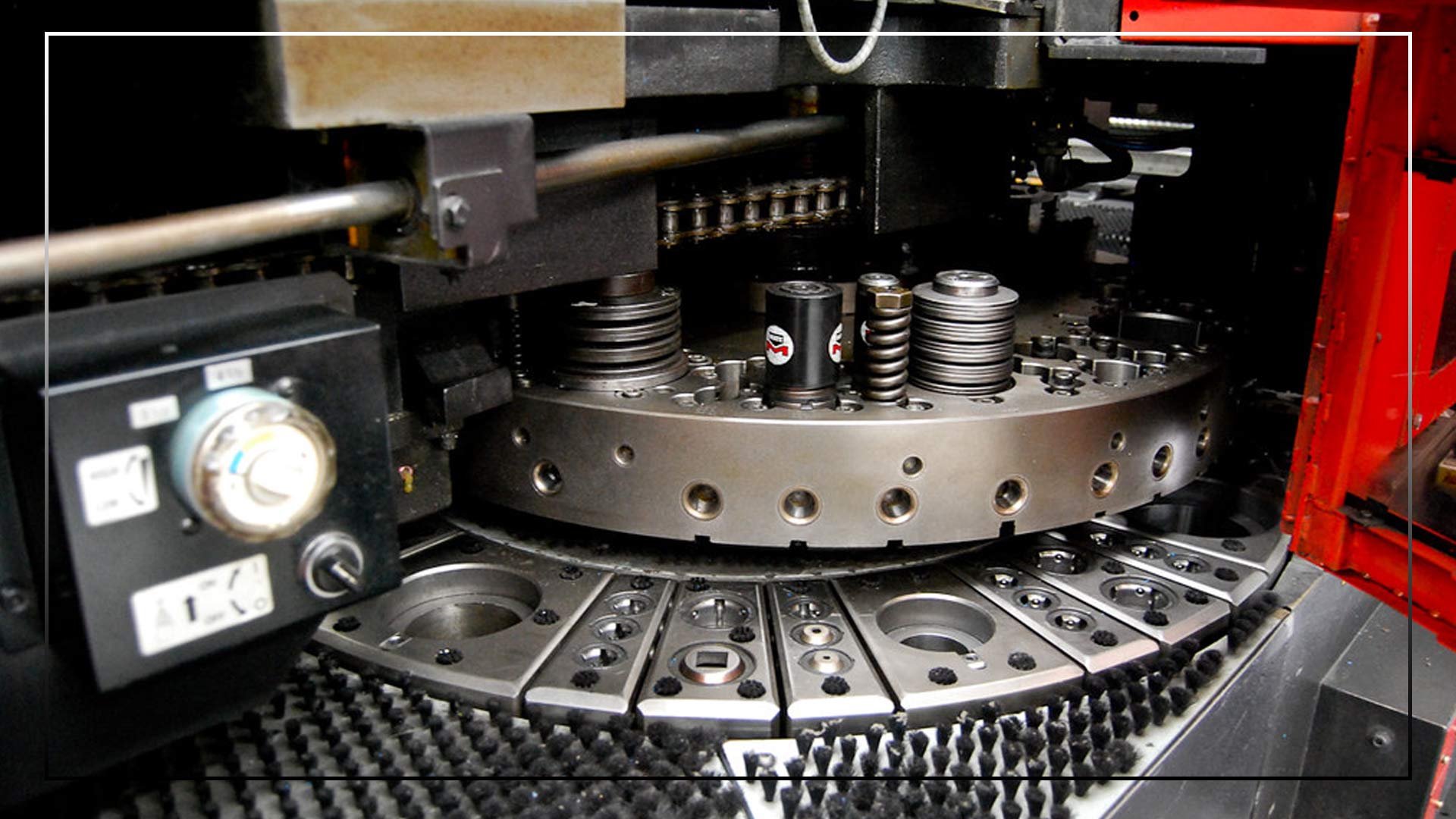
A CNC punch press is the most economical machine used in high volume sheet metal part production. The press is used in fabrication for “punching” shapes into a flat metal sheet. The press operates using paired sets of punches and dies.
The punch is a solid piece of metal that pushes through the sheet metal and into the matching die. The opposing force from the punch and die, when employed correctly, create a clean-cut hole or indentation without deforming the surrounding sheet metal.
At All Metals Fabricating, we use these versatile precision fabrication machines for knockouts, embossing features, lances, countersinks, extruded holes, threaded holes, and much more.
However, we often come across designs that could be improved with simple Design for Manufacturability (DFM) best practices.
Here, we outline a few issues that can arise during production, and provide guidelines on how to avoid them using DFM tips to ensure parts of the highest quality are produced using punching technology.
For your next part requiring CNC punching, reference these DFM tips to reduce costs, save time, and ensure the quality of your parts.
Custom tooling extends lead times and increases costs. Instead, consider designing your part using standard punches the shop has on hand. Custom tooling, if necessary, is always doable, it just takes some time to procure.
Request the tool library from the fabrication shop you’re working with to see your options.
You can find AMF’s tooling library here for Amada and Trumpf.
When designing parts for metal stamping or forming, always consider the volume of parts being produced for the entire assembly / sub-assembly.
For smaller production runs (e.g., less than 1,000 parts), using a consistent material thickness may be more cost-effective and efficient, even if some parts could be made with a thinner material. This uniformity simplifies the manufacturing process by eliminating material handling for multiple material types. It allows all parts to be nested and fabricated together. In doing so, downstream operations can see all the parts and easily ensure that all parts fit together while running.
For larger production runs, the cost savings from using optimal material thicknesses can be substantial. Always balance the upfront effort of process adjustments against the long-term savings in material costs.
Parts with tighter tolerances require more inspection time, skilled labor, and often may require custom tooling to manufacture. Consider loosening tolerances where possible.
When designing parts with both press-in hardware and clearance holes, try using visually obvious different hole sizes to prevent downstream operations from trying to install press-in hardware in clearance holes.
Intentionally adding a tooling change might seem counterintuitive. However, it can prevent common, time-consuming human mistakes later in production.
It is often overlooked, but parts that are “almost” symmetrical can easily be inverted without recognizing it. And more often than not, it is discovered at the final assembly of the product. And by then, the discovery of a nearly symmetrical part being inverted will cause a schedule delay. Nobody wants this. Review all your parts for symmetry, and if they are truly symmetric…awesome! If it is not quite….consider adding a feature like a cutout on one side to make it blatantly obvious to all processes of fabrication which side is inside, and which is outside.
Following our tips for DFM will reduce costs, expedite production, and result in high-quality parts. AMF has state-of-the-art machinery and highly skilled fabricators to take on your next project and exceed your expectations. And don’t ever be afraid to call and talk to any of the account managers, engineers, or programmers about design questions. We are here to help you exceed your expectations every step of the way.
Entrust your next project to AMF’s experienced team. Request a quote.