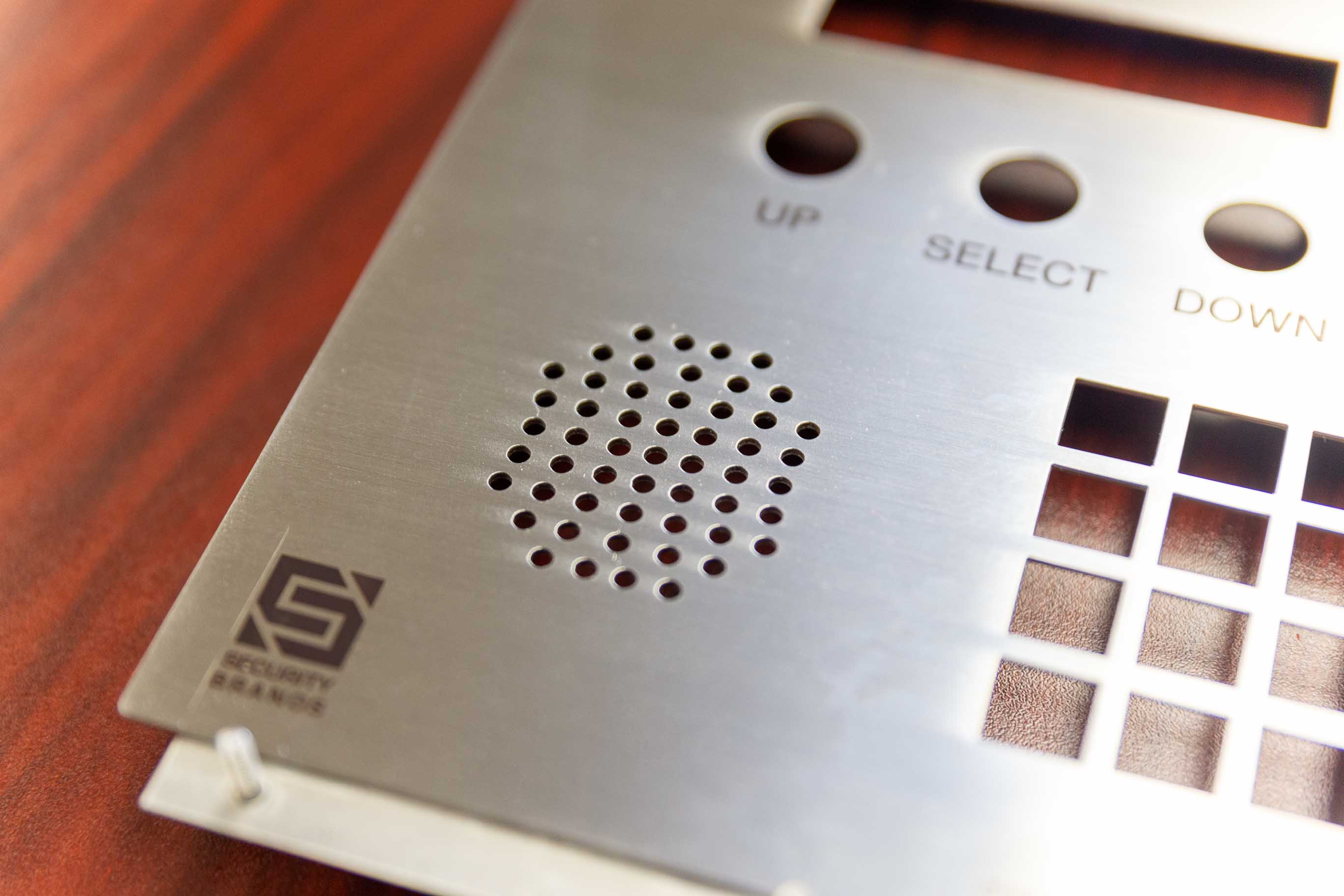
Are you ready to break records with your sheet metal punching and notching expertise?
In any given metal fabrication project, a variety of tools and techniques are employed, and CNC punching is among the best.
Learn more about what CNC punching is, how it works, and how it can benefit you.
CNC Punching stands for Computer Numerically Controlled punching. It is a sheet metal manufacturing process using programmable machines.
CNC punch presses are electromechanical devices that move tools to punch patterns into the sheet metal from a software file using computer programming inputs. These machines are available with a single head and tool rail or a multi-tool turret.
The punch press's programming is based on a few key factors.
The desired pattern is given in either a 2D DXF or a DWG file format or a 3D format in the Computer-Aided Design (CAD) file. This data is then used in the Computer-Aided Manufacturing (CAM) phase of the cycle to choose the best tooling for the job and to fabricate the flat sheet metal component.
The CNC nest will assist in choosing the best arrangement for the sheet metal size.
The sheet metal will then be moved by the CNC punching machine to precisely place it under the punching ram, allowing the required design to be punched and created. Some machines are only able to move in one or two ways, while others can move in all 3 axes.
The materials that can be used in CNC machines are endless; everything from stainless steel, aluminum, brass, wood, plastic, and more can all be punched. The ideal range of thickness that can be machined is 0.5mm to 6mm; thus any material that falls within this range can be punched on a CNC punch press.
The hole choice is versatile, as it can be as simple as a rectangle or circle or can be a specific or particular shape to fit a certain cutout pattern.
Complex sheet metal component shapes can be created utilizing a combination of single strikes and overlapping geometries.
Some advanced machines can tap threads, fold tiny tabs, and punch sheared edges without leaving any tool witness marks, making them extremely productive within the component cycle time.
The CNC program is the set of instructions for driving the machine to construct the specified component geometry.
Once a design has been selected and built, it may be reused time and time again, increasing productivity by getting rid of technical and time-consuming manual operations.
This process is also quick because of the automation and reproducibility; regardless of how complex the design is, the production time is decreased. Precision is maintained, and CNC machines are frequently used for the most complex and precise aspects of machining.
CNC punching machines are fast and accurate while producing less waste. When an internal quality detector, which is found in many machines, detects a defect, the machine will stop punching to prevent further waste.
Because waste is kept to a bare minimum, money is saved in the long run because no raw materials are thrown away. Furthermore, because the entire process is automated, the operator is kept safe while working in a risk-free environment.
Hole sizes should ideally not be less than the sheet metal gauge being CNC punched.
Plunged forms made from parent sheet metal that is unthreaded can help you save money on threaded inserts if the component will be painted. These features, also known as extruded holes, can then be automatically tapped with threads using a tapping tool on the CNC Punch press.
Cluster tools can be used to save even more money on sheet metal work by reducing the CNC punching time for many holes. The tool can include a large number of separate punches, allowing for the punching of thousands of holes each minute.
When perforated features like ventilation regions, speaker grilles, LED panels, or light fittings are being manufactured, these CNC tools can be especially useful.
Part names, issue levels, customer and product names can all be used to identify parts with engraving tools. When fabricating sheet metal for a customer, it's common for them to want to be able to locate the item in their warehouse or in production.
CNC engraving can be a handy solution for identifying sheet metal parts that are utilized in the field for spares and service. Any modifications to the information required by the customer in their part number may simply be reprogrammed when using a CNC punch press to do this engraving.
The capacity to rotate materials during the machining process is what distinguishes this type of CNC machine.
These machines' cutting tools are fed in a linear motion around the perimeter of the revolving bar stock. This eliminates material until the required diameter is reached.
CNC milling machines are distinguished by their ability to rotate cutting tools while keeping the workpiece or block of material motionless.
They may mill a variety of shapes, including shallow, flat surfaces or deep cavities such as slots and threads.
A pointed router with a highly focused laser beam is used in CNC laser machines to precisely cut or etch objects. The laser warms the material, causing it to melt and cutting a hole in it.
The material is usually in the form of a sheet, and the laser beam goes back and forth over it to generate a precise cut.
The use of a CNC punch press operator to operate and configure these electrically powered presses can help you take full advantage of what these machines have to offer.
You can do more project goals faster and more efficiently through the employment of a CNC punch press.
Come check out our page on CNC punching services that can get you started.