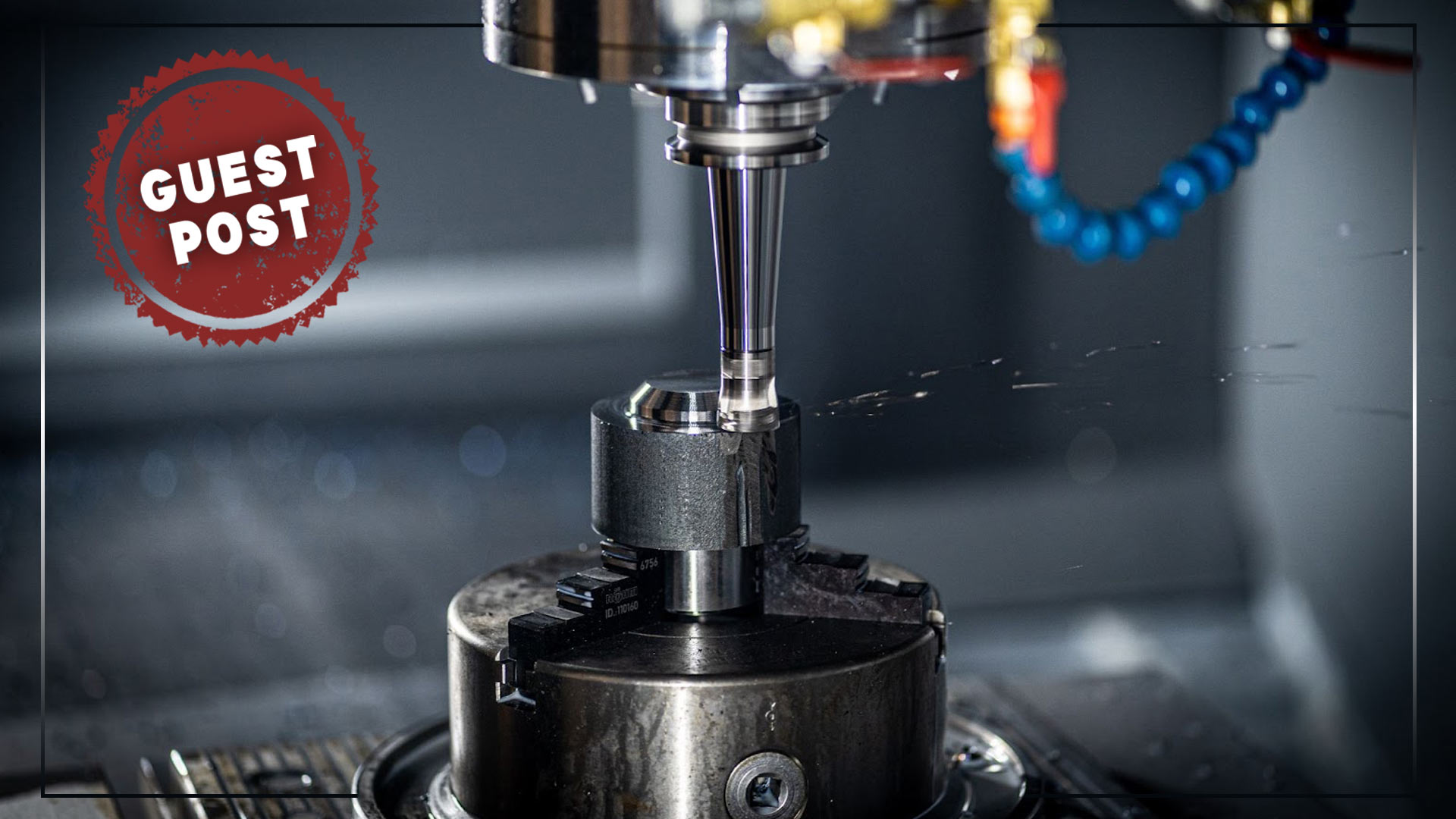
Material selection is a critical decision in any manufacturing project. The choice depends on a variety of factors, from strength to weight to price, and the ultimate decision will have a major impact on the project’s success.
At All Metals Fabricating, we have extensive experience with a wide range of materials in both precision fabrication and CNC machining. This is a guide to some of the manufacturing materials we work with most frequently, and why All Metals is the perfect partner to complete your next part.
Stainless steel has a variety of well-known benefits. It’s a strong material, it’s very rigid, and it’s corrosion-resistant. Stainless steel is a relatively expensive material, but in many use cases, the benefits make the price worthwhile. It’s great for structural or outdoor applications, for instance. Even in indoor applications, it’s often perfect for use cases when finishing or corrosion is a concern. While some of our customers do passivate their stainless steel parts, you won’t need to plate it or powder coat it. This can create cost savings in a project despite the initial material expense.
There are several different grades of stainless steel, and at All Metals the two we see most often are type 304 and 316. Type 316 is often used for outdoor applications because of its strong anti-corrosion properties.
There are also several different finishes available for stainless steel. Among the most commonly requested in our metal fabrication shop are No. 2B, No. 3, and No. 4, with each varying somewhat in appearance, corrosion resistance, and surface texture.
Fabricating and machining stainless steel can be tough on tools, which often results in higher quotes for parts made from this material. If at all possible, it’s often simpler and cheaper to use aluminum, which has similar corrosion-resistant properties. If you are using stainless steel for parts, it’s often best to use a softer grade like 303 stainless. But if your part requires 316 stainless steel or stronger, we can always make it happen.
Finishing stainless steel is one of our shop’s strengths, allowing us to take on projects other shops can’t or won’t. Our team of metalworkers apply a range of finishes, and they can even restore the original No. 3 or No. 4 finishes on welded parts.
At All Metals, we typically have every common gauge of 304 and 316 already in stock. Other shops often do not stock as much stainless steel because they hesitate to invest in the material upfront. But when you work with All Metals, our extensive stainless steel inventory will reduce your lead time and allow you to save on material prices because of our purchasing power.
Aluminum, like stainless steel, is corrosion-resistant, one of its major benefits. In comparison to stainless steel, it’s more lightweight, more cost-effective and easier to fabricate and machine.
For sheet metal fab, we most commonly work with 5052 or 6061. 5052 is typically the better option for sheet metal, because 6061 can have cracking in the bends without properly sized radii. But at All Metals, we’re capable of using both materials and if 6061 is better for your project, we’re happy to use it.
For aluminum CNC machining, we most often see 2024, 6061 and 7075. All of these aluminum alloys are far easier on the tooling than stainless steel, which allows machines to run at the highest RPMs.
Aluminum is occasionally finished with chem film, anodizing, or powder coating if it will be used in outdoor applications.
Aluminum is a more challenging material to weld, which is why many shops avoid aluminum welding projects. But at All Metals, all of our certified welders can tackle any MIG and TIG aluminum welding project, even thin gauge.
We stock every common thickness of 5052 and a variety of 6061. Just like our stainless steel stock, our existing aluminum inventory can improve your lead times and lower your material prices.
Steel is a versatile material used in both sheet metal fabrication and CNC machining. While there are many types of steel, the basics are simple: steel is strong and affordable.
At All Metals, we stock A36 steel and 1018 steel in all common gauges, both hot-rolled and cold-rolled. Hot rolled is less expensive than cold rolled, but it is not as cosmetically appealing, The differences, however, are minimal and often non-existent after finishing.
Steel will rust, so customers typically plate it or powder coat it for corrosion resistance. Alternatively, some customers will plate, wet paint or hot dip galvanize it, depending on the application. Some customers may perform multiple finishes on their steel parts, but it’s worth noting that, after multiple finishes, the cost may approach levels close to stainless steel.
Within the context of All Metals Fabricating, galvanized steel essentially refers to a pre-galvanized sheet. This material is rarely used in machining and instead is primarily for sheet metal fabrication.
Galvanized steel is strong, but the greatest benefit of this material is its low cost and also has fairly attractive finish. Galvanized steel is also corrosion-resistant, though it's important to note that any cut edges expose raw steel, which can rust if used outdoors without proper finishing. For indoor use, galvanized steel is ideal, as it typically requires no additional finishes.
Galvanized steel is often valued for its reflective properties, and is used in radio frequency (RF) shielding applications such as RF chambers. We typically have between 10 gauge and 20 gauge galvanized steel in stock at our facility.
Galvanized steel can be dangerous to weld, but at All Metals we have the equipment and the expertise to safely and efficiently handle this task. We have specialized helmets and welding equipment for galvanized materials, as well as proper ventilation to prevent dangerous levels of fumes. Many shops simply will not weld galvanized steel, because the fumes are too dangerous and they don’t want to invest in the specialized equipment required.
At All Metals, we frequently work with copper, as it is an essential material for many electrical applications. While copper is easy to machine and naturally corrosion-resistant, it is relatively expensive and its price can be volatile. Copper naturally develops a patina when exposed to the elements. To prevent this, some of our customers opt to tinplate their copper parts, depending on the application.
We stock most common thicknesses of copper at our Texas sheet metal shop. For instance, we frequently fabricate copper bus bars, so we maintain a large inventory of 1/4" and 3/16" copper sheets for this purpose.
We have an eight kilowatt fiber laser, allowing us to cut up to 3/8” copper, and we can also cut it by using a punch press.
Choosing the right material is key to the success of any manufacturing project. At All Metals Fabricating, we bring extensive expertise to working with a variety of materials such as stainless steel, aluminum, steel, and copper. We also excel in fabricating and machining plastics and other exotic materials. Our comprehensive capabilities, fleet of equipment and deep material inventory allow us to deliver high-quality results efficiently, making us the perfect partner for your next project.
Request a quote from our team today.