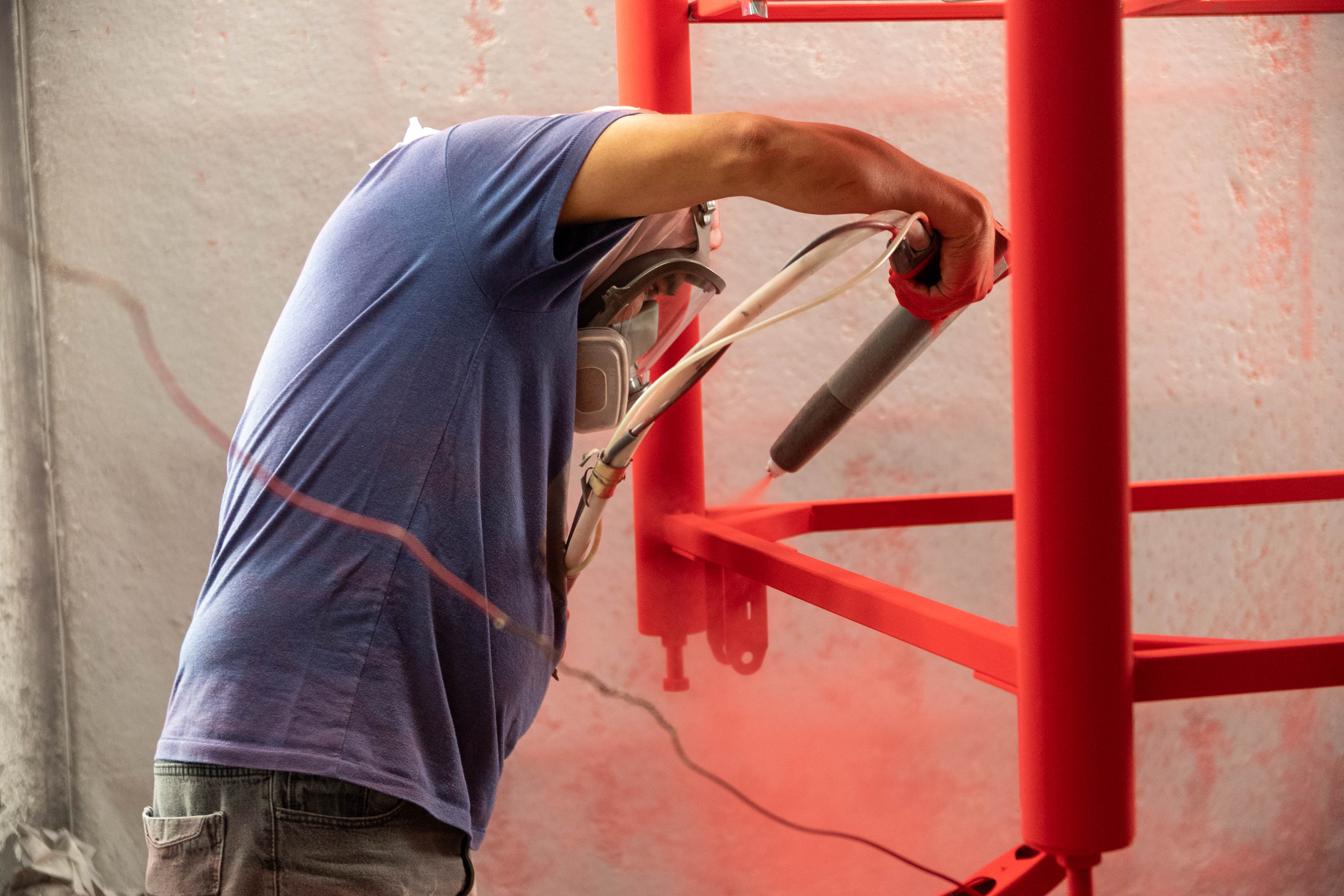
Metal parts fabrication demands the implementation of distinct technologies and approaches. Metal fabrication shops such as All Metals Fabricating have a wide range of CNC machines and other equipment to facilitate complex processes that involves getting familiarized with casting, machining, forging, and plating.
The manufacturers must be well acquainted with the properties of different metals, their alloys, and part finishing to ensure that metal fabrication gets executed at a high-efficiency rate.
According to specialists, metal fabrication is the implementation of bending, cutting, and assembly to manufacture metal components. Metal fabrication helps produce items, such as irrigation pivots, precision-engineered jet engine parts, and metal stanchions for livestock.
Several processes contribute towards metal fabrication, which may or may not be required to produce different parts. However, fabricators keep their options broad and open to create distinct mechanical assemblies.
Here are some typical processes involved in metal fabrication:
If you run a small-scale business, it is advisable to be economical and use small CNC mills. These mills are not only light on your pocket but also deliver decent efficiencies, implying that you do not have to compromise on quality while being economical.
Here is a detailed overview of the various processes involved in metal fabrication and their respective significance:
All manufacturers use forging to create intricate metalwork. It involves the use of forced compression to bend the metal in the desired shape. The metal gets heated until it can be bent and reshaped using a hammer or die strike.
Forging is a commonly used practice employed by blacksmiths and fabricators to render complicated and artistic designs to the metal piece.
While forging is done by hand, casting involves pouring the molten metal into a mold. After pouring, it is left idle to cool down, so it becomes hard.
Casting is the fundamental process for the mass-production of products where manufacturers can use the same mold repeatedly with minimal distinction in the eventual outcome.
This fabrication process involves using tensile force to pull the metal into a tapered die. This process involves stretching the metal into a thinner shape.
Drawing is typically employed in sheet metal fabrication processes where the ultimate product is a box-like or cylindrical vessel.
Forming involves bending the metal and giving it the desired angle. This process can be accomplished using a brake press that applies pressure to metal to form a crease.
There exist other forms of folding as well, which can get done using a hammer with clamp bars to ensure that the metal piece stays in place.
Machining is a subtractive shaping process that helps remove redundant metal to create a form. There are several different forms in this substrate, such as drilling, milling, and turning.
Turning involves using a lathe to rotate the metal at certain speeds to enable the cutting tools to remove the metal circularly. For high quality results, A CNC machine is typically used for lathe-turned products using precise measurements.
Milling is one of the most common processes among other metal fabrication techniques by which multi-point cutting tools take out metal from the workpiece.
Manufacturers use CNC machines for milling, which operates as a final finish process to deliver a specific texture or appearance.
In the process of extrusion, the metal piece gets forced between an opened or closed die. Here, the metal piece gets cut down to the cross-section of the die leading to the formation of a cavity.
Cutting is one of the most versatile metal fabrication processes. While on the surface, it might appear nothing more than cutting enormous pieces of metal into smaller bits.
Cutting is an intricate process; however, to streamline workflow, automation that involves lasers, power scissors, waterjets, and plasma is utilized to produce exacting cuts.
Punching involves creating holes in a workpiece. Punch presses come with specially designed turrets to hit the metal through a die and form holes in precise locations. Punching is involved in light and bulky metalwork.
Stamping involves creating indentations in metal rather than holes by using a press or handheld hammer. Some of the most popular applications for stamping involve creating letters, images, and shapes.
To exercise precision control over acceleration, linear/angular position, and velocity when working on a CNC machine, ensure that your shop has the best quality servo motors available, which help obtain optimum results.
Welding involves adjoining two or more metal pieces using a mixture of pressure and heat. This process is commonly implemented at an extensive scale or industrial fabrication projects.
Welding is so prominent because several metal pieces can get conjoined regardless of their shape or size. According to each specific project, some of the most common weldings are stick and arc, MIG, TIG, and flux-cored arc.
It is imperative that the manufacturers truly comprehend the processes and materials involved in metal parts fabrication due to their unique and highly detailed characteristics. All Metals Fabricating This guide can help you grasp the various processes involved in fabricating a metal piece with extreme intricacies.
About the Author:
Peter Jacobs
Peter Jacobs is the Senior Director of Marketing at CNC Masters. He is actively involved in manufacturing processes and regularly contributes his insights for various blogs in CNC machining, 3D printing, rapid tooling, injection molding, metal casting, and manufacturing in general.