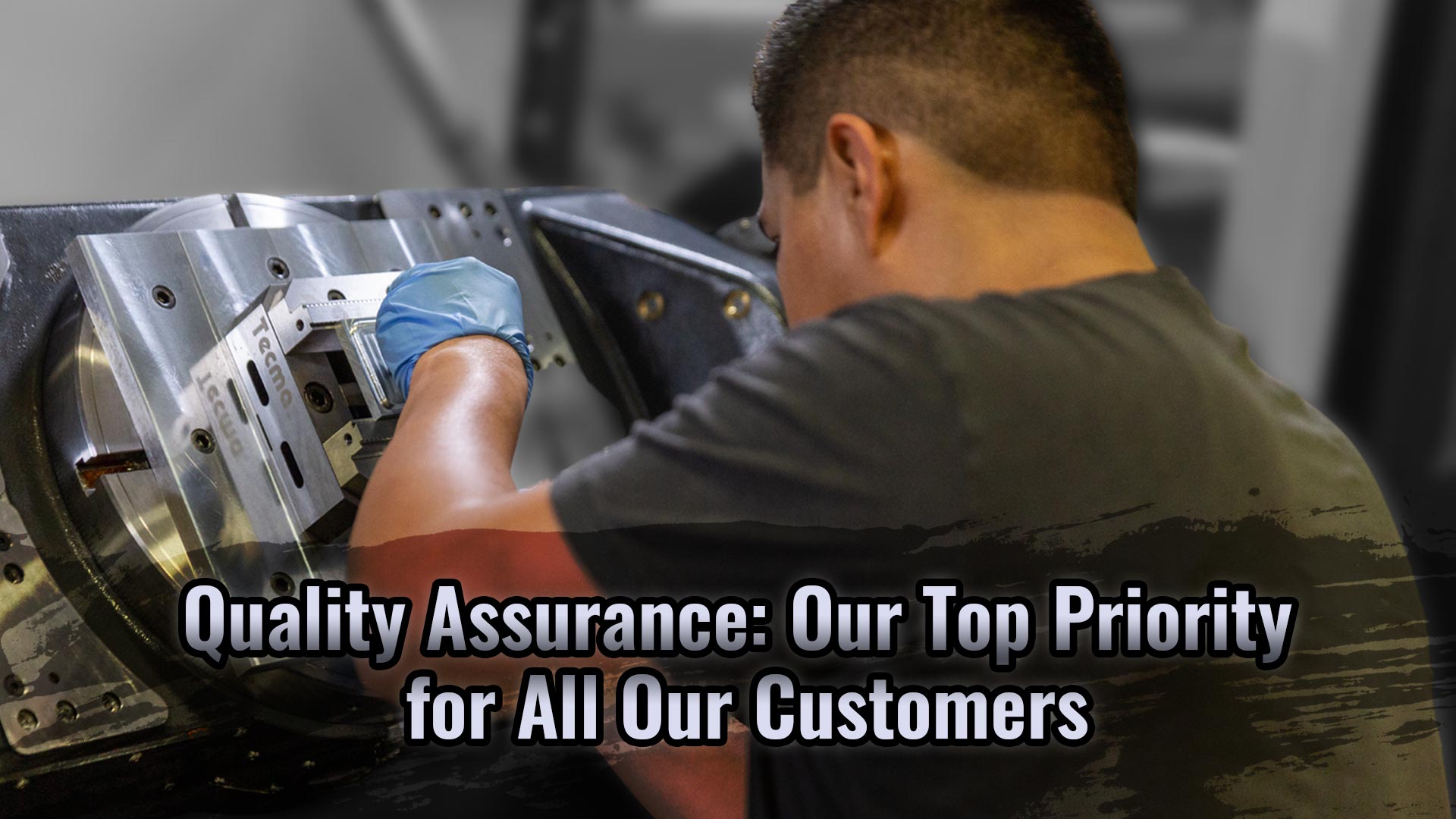
At AMF, quality assurance isn’t just the responsibility of a separate department or tacked on at the very end of our precision fabrication process. Quality checks are built into every process and owned by each employee. All of our team members are committed to creating quality parts, from account managers to fabricators to welders to shipping.
And we have the right equipment to ensure superior results. We invest in new technology to ensure we’re using the most efficient and precise tools on the market.
Even part rejects become a lesson on quality for everyone involved. We look at where parts went wrong and have a conversation with each department that touched the part after the mistake to prevent and catch errors from happening again.
Everyone makes mistakes, but at AMF, we’re committed to learning from them—and building corrective actions to prevent them in the future.
In the AMF process, quality checks begin before manufacturing even begins. To hit the ground running, our programmers load flat patterns into CAD software and submit them to our quality department, where they are compared with the prints. Once approved, our programming department uploads the flat patterns to our inspection equipment.
After manufacturing the first part in an order, the operator uses our InspecVision machine to measure the part and check it against its flat pattern. Once the part’s geometry is validated, manufacturing can continue.
We continue to check the quality of the first part. If we’re working on a first-time build, our quality department will review the part after each operation before the final inspection to add an extra level of assurance. After the rigorous first pass, we streamline the process by having department heads check off on established parts. Each operator is also responsible for checking parts based on our sample plan, C=0, throughout their process.
Further, we train everyone that each department is a customer/vendor relationship, and that they are “buying” the parts from the previous department. Hence why, in the event of a rejection, we engage each department that touched the parts after the mistake was made to show them that they bought off on a non-conforming part.
These continuous quality checks ensure we meet the rigorous standards expected of our precision fabrication shop. We are proud to say that we consistently achieve over a 99% order acceptance rate and a 99.6% PPM acceptance rate. When customers work with us, they can be confident in the high quality of finished parts and the efficiency of our system.
The tools we use to perform quality checks are integral to our quality control process. The InspecVision, which validates the geometry of a part, is our most critical piece of inspection equipment. But we utilize other tools in our quality control process:
We calibrate all in-house quality equipment and tools regularly per ISO requirements to maintain ISO compliance and ensure consistency and reliability.
Our thorough inspection processes and world-class equipment enable us to deliver quality products, but we couldn’t maintain such a high standard of quality without a team of dedicated employees. Every AMF employee helps us build solid customer-vendor relationships by keeping quality at the forefront of their minds—and quality is what we deliver.