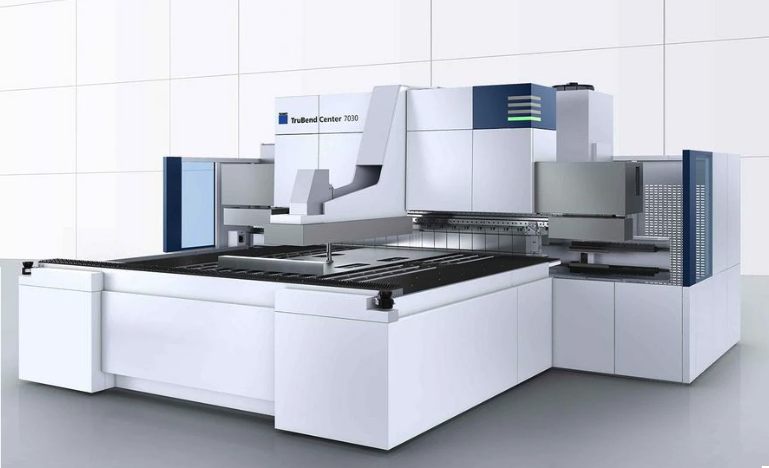
Are you looking for a small part sheet metal fabrication service that is fast and efficient? Do you want to use state of the art technology in your sheet metal fabrication firm to increase production? In both of these cases, you could benefit from the TruBend Cell 7000.
A compact machine designed for quick, automated processes, the TruBend is a marvel for anyone creating or needing small parts manufacture. Read on to find our must-know guide to this amazing piece of equipment.
The TruBend Cell 7000 is a market-leading machine bending system, designed for small and compact areas. Despite its small size, it remains efficient and dynamic. It is the fastest small part bending cell, due to its dynamic drive concept and backgauges.
The system facilitates automatic production methods. It has flexible storage options with its conveyor system. The items produced are automatically placed in boxes or have the option for removal and placement onto a conveyor system.
Tools can change automatically with an advanced Toolmaster bend system, meaning the device will change its own production tools as it works. This can save time and allow for much quicker production runs.
A mechanical gripper enables automated bending by using its rotary and linear regripping ability. It also has a self-cleaning service, reducing further maintenance on your part. The Loadmaster bend function facilitates and optimizes material flow as it works parallel to production.
Parts up to 20x15 can have precise angles and measurements. In fact, the automatically controlled bending angle measuring system gives constant precision. It ensures perfect angles, with communication between the tool and control so the self-correction of incorrect angles is automatic.
While the machine is automated, it does require programming and maintenance.
That is where effective training comes into play, and the manufacturers, TRUMPF, provide a thorough training regime for the correct operation of the system. They have a range of bending machines, and further education regarding each and every one of them is encouraged.
The machines are manufactured by TRUMPF, specialists in machine bending equipment. They aim for sheet metal fabrication equipment that results in quality, with no scratches or marks. This uses their automatically controlled bending system (ACB), which manages to work quickly and efficiently.
Tools produced are created by the company themselves. Over 150 standard tools are already made, so you can count on expert advice, quick availability, and the option to have custom tools built if you need them. Due to a laser hardening process, all tools are also durable.
A machine can function around the clock if need be, increasing productivity. The customized tools work in conjunction with a choice of conveyor belts and pallet conveyors. This allows for a tailored material flow that can complement the manufacture of tools on the production line.
TRUMPF has specialist bending software known as TruTops, which can program the bending of parts independently. They can adapt to the specialisms of programmers on your team. Programs are reusable, so they take the same amount of time if you are doing a small or large run.
Programming for bending cells is done offline. They are created at a workstation that runs parallel to production. It frees up staff, reduces non-production time, and increases the availability of the machine.
Intelligent programming in the TruTops Bend program calculates the optimum bending solution. It can select the best tools for the job and calculates the best bending sequence. High-tech algorithms can work out the most efficient traverse paths for you.
This can be overseen by TruTops Calculate, to save time and cash. It can provide anticipated times, along with the cost for parts and materials, including the entire assembly line. You can also include specific cost requirements, such as labor costs, profit margins, and machine hour rates.
Manual setup takes a lot of time. TRUMPF has recognized this and uses the Toolmaster automatic tool to set up a system that switches equipment automatically in the blink of an eye.
Not only does it mean less work for your operator, but it also saves time and allows for increased production.
The standard tools come as a set or individually, making it easy to adapt to any kind of job or situation. There are currently 150 upper and lower tools available. These can be easily loaded into the control using a data matrix code.
A series of lightweight tools are also available. These can be up to 35% lighter than regular tools.
Guaranteed precision comes using many sensor tools. These are sensor discs integrated into the shape of the tool. All of this works according to an ACB system.
Unwanted adhesions will not occur due to particles of aluminum and zinc sheet abrasion. This is down to high-quality coatings and the surface hardness of the tools. These tools do not need cleaning and are resistant to corrosion.
A RollBend tool allows short flange lengths, low mark holes, and the creation of moldings, even close to the bending lines. These can be done without any deformation, and with molded elastomer layers bending is mark-free.
Now you know the benefits of the TruBend Cell 7000 for small parts manufacturers, you need to find a facility that houses one. Contact them for a quote and discuss your requirements.
All Metals Fabricating has been serving complete manufacturing solutions since 1953. We have a range of precision devices and machine servicing for all your business needs. Contact us today to discuss your requirements and let us provide a quote from one of the most trusted providers in the business.