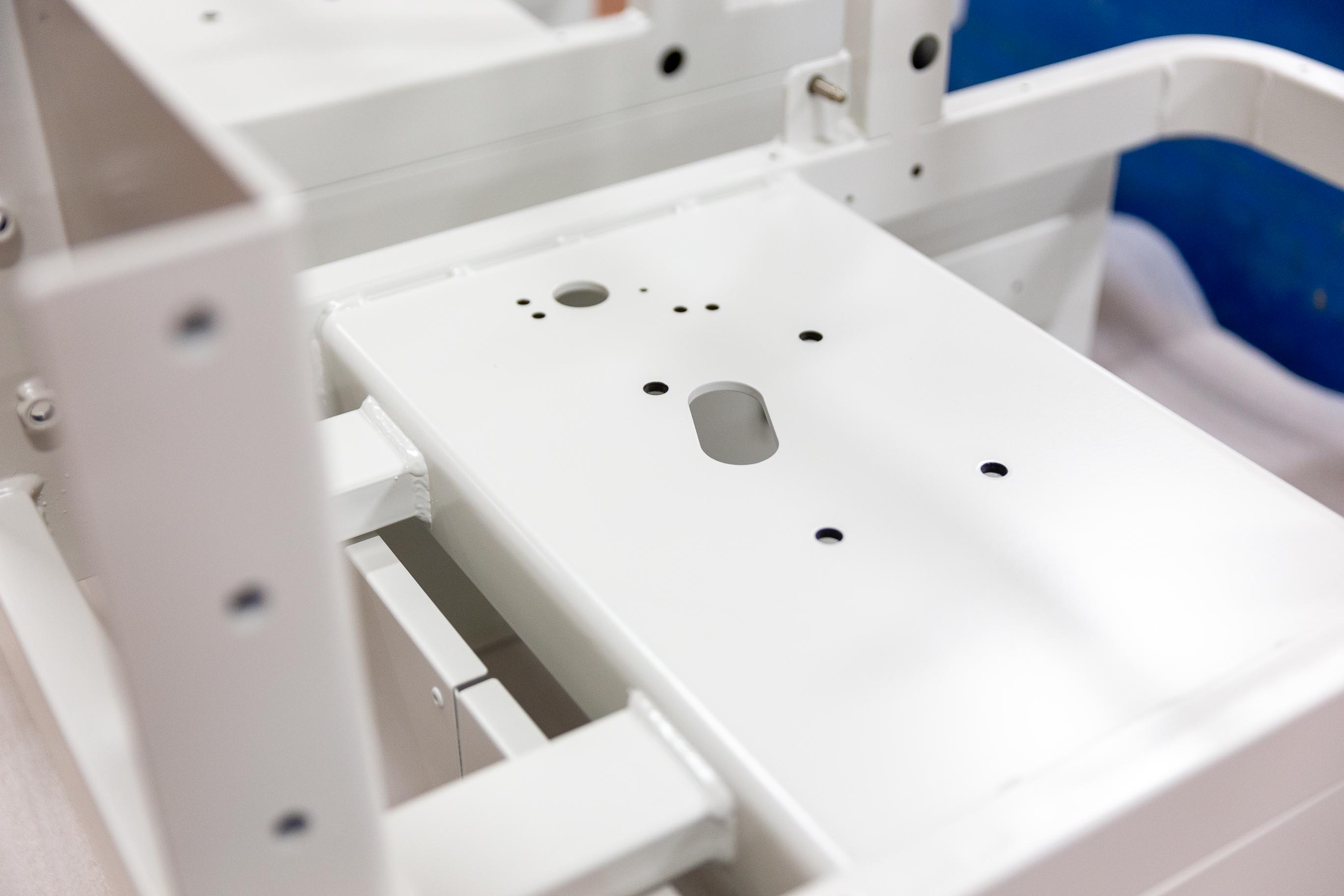
Steel is one of the most common materials used in precision sheet metal fabrication because of its strength, durability, and corrosion resistance. This versatile metal can be treated in several ways depending on the finish, intended use, and more.
The steel type you select can make or break your part’s success, so it’s important to understand the nuances of each process. We’ll break down the characteristics, applications, and cost implications of the two primary steel treatments, hot-rolled and cold-rolled, and share our advice from over 70 years of experience in Texas sheet metal fabrication.
Hot-rolled and cold-rolled steel are the two most common steel treatments we see in our Texas sheet metal fabrication shop. Steel manufacturers heat large, rectangular pieces of steel to 1,700 degrees Fahrenheit, then roll the steel through the mill to reach the desired shape.
Both hot and cold-rolled steel go through this process, but cold-rolled steel is re-rolled at room temperature for further compression.
Each treatment has benefits and drawbacks, but we generally find that hot-rolled steel is the more cost-effective choice.
Hot-rolled steel is easily identified due to its scaled surface, slight distortions, and rounded edges. These imperfections develop as the metal cools down. Hot-rolled steel may require decarburization or other surface treatments to prepare it for subsequent operations.
Despite its rough appearance, hot-rolled steel has several advantages:
There are, however, some downfalls associated with using hot-rolled steel:
When customers work with All Metals Fabricating, our commitment to quality shines through. We source high-quality hot-rolled steel that will never have pitting, even when working with thicker sheets of steel.
Hot-rolled steel is suitable for many applications due to its cost-effectiveness and structural integrity from minimal processing. Powder-coating will increase the steel’s durability, even in extreme weather and under physical stress.
However, steel manufacturers have less control over the final shape, so hot-rolled steel is generally used for parts that don’t require tight tolerances.
Here are several applications where hot-rolled steel is ideal:
Unlike hot-rolled steel, cold-rolled steel is aesthetically pleasing, with a smooth and shiny surface that feels oily to the touch. The additional processing also creates perfectly squared angles with well-defined corners and edges.
Cold-rolling steel has many benefits, including:
Despite its superior appearance, there are several downsides to using cold-rolled steel:
The refined appearance of cold-rolled steel makes the cold-rolling treatment ideal for parts without surface finishes. The additional round of processing gives steel fabricators greater control over the final size of the sheet metal, so precision sheet metal fabrication parts requiring tight tolerances should use cold-rolled steel when possible.
Here are a few examples of applications that benefit from cold-rolled steel:
While hot-rolled and cold-rolled steel are the most common treatments in contract manufacturing, there are several alternative types with more specific applications:
Stainless steel is stronger than hot or cold-rolled steel, and it is much more weather and corrosion-resistant. This treatment is ideal for outdoor applications, especially near coastlines where corrosion from salt is prevalent.
Galvanized steel has a protective layer of zinc applied to the sheet. This material is long-lasting, making it an excellent choice for hard-to-reach applications like phone lines and equipment boxes. However, cutting galvanized steel exposes the raw steel, necessitating additional treatment for outdoor use.
AR500 steel is one of the hardest treatment types available. However, it’s also incredibly rigid, making it difficult to form. Steel with this treatment is most often used for targets in shooting ranges.
This treatment type is ideal for outdoor architectural and landscaping applications. Corten steel is also known as weathered steel because when left outside, it will develop a rust-like appearance, which provides a protective layer from corrosion and atmospheric elements.
Selecting a steel treatment is all about balance and finding the best fit for your part. For example, hot-rolled steel is often more cost-effective, but you likely should go with cold rolled steel if cosmetic appearance is important to you.
There are many considerations that go into choosing which type of steel to use! The AMF team has over 70 years of experience in selecting the best steel treatments, and we are always happy to work with customers to find the best solution for their parts.
Request a quote today to get started.